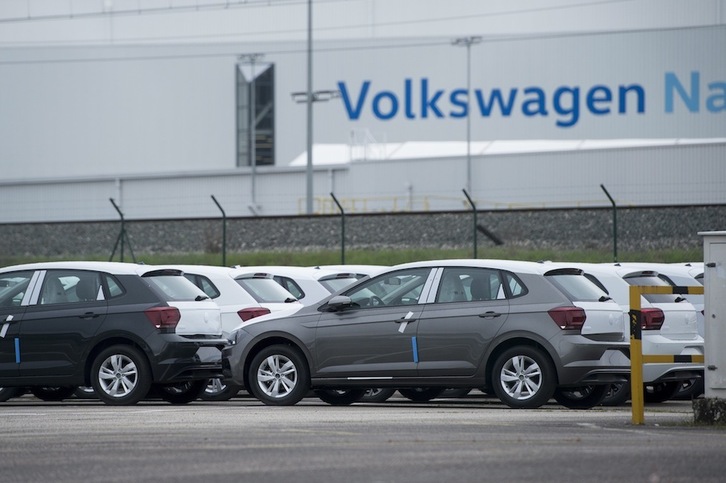
Volkswagen Navarra ha desarrollado, de la mano de las empresas Asti y Autocar, un novedoso sistema de logística, para la organización de la secuenciación y traslado de las piezas a la línea de montaje, que se basa en el empleo de vehículos autónomos y en la digitalización de todo el proceso.
Se trata del primer proyecto de estas características aplicado en una de las 32 fábricas de la marca VW, lo que coloca a esta planta a la cabeza de la automatización logística en el conjunto de la compañía, según ha informado este viernes en un comunicado la dirección de la empresa en Nafarroa.
El sistema concierne a la parte del proceso logístico donde se secuencian las piezas de la línea de montaje para los tres modelos que produce actualmente la factoría de Landaben: Polo, T-Cross y Taigo.
La principal ventaja del sistema, además de la propia automatización, consiste en el mayor aprovechamiento del espacio, lo que contribuye a no tener que recurrir a almacenes externos por la producción del tercer modelo, el Taigo.
«No se trata tan solo de un cambio de proceso o de un proceso típico de automatización. Es algo mucho más profundo que ha provocado una transformación radical en la forma de trabajar. Sin duda, supone un paso de gigante hacia la logística autónoma», ha indicado Alfonso Eslava, director de Logística.
Pedidos al «supermercado»
El proceso comienza con la solicitud de material en el punto de montaje, que llega de forma digitalizada a la zona de secuenciación (conocida internamente como ‘el supermercado’), donde un operario secuencia las piezas en el orden preciso colocándolas en carros especiales.
Estos carros se suministran mediante vehículos autónomos (AGV), que a su vez gestionan su retorno cuando están vacíos.
Cuando el trabajador que realiza la secuenciación necesita reponer el material, lanza una petición al almacén, que se tramita de forma paralela al sistema que gestiona los AGV, para que estos se encarguen de retirar el contenedor vacío y realicen la reposición del lleno, colocado previamente por un carretillero en la zona de transferencia.
Eslava ha explicado que «el gran reto de este proyecto ha sido la aplicación de una tecnología ya existente al sector de la automoción, donde la velocidad de las líneas de Volkswagen Navarra hace que el nivel de exigencia y disponibilidad del sistema sea altísimo, ya que suministramos carros con piezas secuenciadas a razón de 1,5 por minuto».
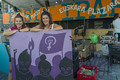
«Hau ere bada erreibindikazio bat, geureak diren kaleak berreskuratzearena»
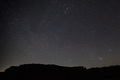
¿Cómo ver las Perseidas? La lluvia de estrellas que no te puedes perder
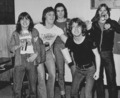
AC/DC: El origen de una leyenda contada desde los márgenes
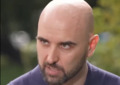
«En Polonia me torturaron e indujeron al suicidio»; entrevista a Pablo González en Rusia
