
El reto que se habían marcado los fabricantes era equiparar, en un plazo relativamente razonable, el precio de un coche eléctrico con el de uno convencional. Algunas marcas lo estaban empezando a conseguir, con modelos por debajo de los 20.000 euros, como el Dacia Spring.
Pero este 2022 ha surgido un problema inesperado, que no es otro que el encarecimiento de las materias primas con las que se fabrican las baterías. En lo que llevamos de año, el precio del litio, uno de los materiales empleados para fabricarlas, ha aumentado en más de un 500%, rompiendo una tendencia a la baja que se prolongaba durante la última década.
Todo ello está provocando fuertes tensiones en la industria automotriz, ya que podría echar al traste el proceso de adaptación hacia la movilidad eléctrica. Con el fin de que esto no suceda, los principales fabricantes se han lanzado a una carrera para buscar acuerdos en exclusiva con empresas mineras que les garanticen el suministro. Incluso no descartan comprar directamente alguna compañía extractora.
Tesla, que con 936.000 unidades vendidas en 2021 es el principal actor en ese mercado a nivel mundial, ya ha anunciado un acuerdo por tres años con la china Gan feng Lithium, el mayor proveedor mundial de litio, para garantizarse el suministro. GM y BMW también están invirtiendo en la extracción del «oro blanco» en California y en Argentina, y tanto VW como Mercedes han tomado posiciones en Canadá, donde hay una gran fuente del mineral sin explotar.
Pero todo ello no ha impedido que algunos fabricantes hayan comenzado a revisar al alza los precios de venta de sus coches, lo que deja en evidencia que su rentabilidad es cada vez más difícil. El mejor ejemplo de ello lo encontramos en el Volkswagen ID.3, el modelo con el que la marca alemana pretendía democratizar el coche eléctrico, y cuyo precio no para de subir. De los 38.300 euros que costaba hace un año, pasó a los 41.000 del pasado mes de julio y a los 42.450 que cuesta en este momento (versión con batería de 58 kWh y 150 kW de potencia).
Otro modelo que todavía no ha salido al mercado pero que iba a costar menos de 20.000 euros, el VW ID.2 (que se fabricará en Landaben), tendrá ahora un precio «inferior a 25.000 euros», tal y como se ha visto obligada a corregir la compañía alemana. Y otro ejemplo muy clarificador lo constituye el Ford Mustang Mach-E, cuya fabricación es ahora 25.000 dólares más cara que un SUV con motor térmico equivalente, lo que ha llevado a los responsables de la marca a reconocer que ya no es rentable.
Mayor tiempo de espera. Otro de los problemas que amenaza la expansión del coche eléctrico es el mayor tiempo de espera que se acumula para su entrega al cliente, con demoras de hasta siete meses de media frente a los cinco que se requiere para los automóviles con motores de combustión, puesto que se necesitan más microchips para su fabricación.
Las marcas europeas y estadounidenses sienten más los efectos de estas dos crisis solapadas, debido a la ausencia de proveedores propios, en tanto que las asiáticas, que sí tienen sus canales, están teniendo menos problemas de producción, aunque tampoco se libran de los retrasos.
Y por si esto fuera poco, no hay que perder de vista la escalada en los precios de la electricidad, que está haciendo que la recarga de las baterías resulte cada vez más cara. La tormenta perfecta está servida.
Dudas ante la nueva generación de baterías
El encarecimiento de las materias primas ha llevado a los principales fabricantes de automóviles a buscar nuevas tecnologías alternativas que permitan rebajar su coste, como las baterías de estado sólido, de mayor densidad energética, aunque de momento solo existen prototipos.
Lo que sí se han empezado a montar en algunos coches –Tesla y BMW, principalmente– son las baterías cilíndricas 4680 de iones de litio (en la imagen), cuya principal virtud consiste en que son más baratas y eficientes. Las nuevas celdas se caracterizan por ser más grandes –tienen un diámetro de 46 mm y una altura de 80, de ahí su nombre–, y son capaces de almacenar cinco veces más cantidad de energía y de otorgar hasta seis veces más potencia. Todo ello con una mejora de la autonomía y de la velocidad de carga. La distribución de los electrolitos, mucho más simple que en los diseños convencionales, es lo que permite abaratar los costes de producción.
Pero no todo son ventajas. Según se ha sabido recientemente, su reparación resulta muy costosa, ya que las celdas se integran directamente en el chasis siguiendo el nuevo concepto de batería estructural, que permite liberar espacio para la batería pero al mismo tiempo se convierten en parte de la estructura del vehículo.
La consultora de ingeniería norteamericana Munro Associates, especializada en desmontar aparatos tecnológicos, ha comprobado que resulta prácticamente imposible reemplazar las celdas dañadas de las baterías que Tesla está instalando en los últimos Model Y, ya que están cubiertas con unos paneles de plástico sellados con gruesas capas de una resina similar al poliuretano. De tal forma que el cambio solo se puede realizar rompiendo dicho paquete, lo que obliga a encargar una batería nueva.

«No se hunde la oferta, cada vez se firman más alquileres temporales fraudulentos»
«Tenemos 58 personas saliendo de prisión cada día, hay que fortalecer Harrera»
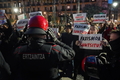
Afari solidarioen aurka egin zutenen aurrean, «faxistak kanpora» oihuak Donostian

El caso Cabacas, «insuficientemente clarificado» según el memorial inaugurado en Bilbo
